Warehouse and Logistics
Logistics and industrial space has been at a premium for some time and this demand looks set to continue. Developers are under pressure to deliver high grade warehouse units in even shorter timescales.
Building occupiers are expecting units to align with their corporate environmental, social and governance policies which means they are required to be increasingly energy efficient, to reduce carbon emissions, increase employee well-being and improve operational efficiencies.
Thorlux are well positioned to assist developers and building occupiers with their ESG obligations, whilst also helping to achieve BREEAM Excellence, compliance with well building standards and much more.
Warehouse and Logistics Application GuideAreas
The Challenge
Distribution warehouses come in all shapes and sizes, but all have a common work process: goods are received, stored and then despatched. The storage period can vary from a few hours to weeks or even months. It is a pre-requisite that goods are not damaged whilst in storage and when required can be located quickly for speedy despatch.
Where high-value goods are stored in bulk, accidental damage needs to be avoided. Therefore, good lighting is essential to ensure they are moved safely and without damage.
Lighting management systems
Within warehouse applications lighting can be a significant part of the energy consumption. Large, bulky buildings use high output luminaires and energy is often wasted by leaving all areas fully illuminated when not occupied. The SmartScan lighting management system makes the most of maintained illuminance, daylight dimming and presence detection to ensure optimum energy savings, often measured in real applications to exceed 70%. SmartScan also monitors the performance of all luminaires so any fault can be reported promptly to the maintenance teams.
Find out moreEmergency Lighting
The extent and nature of the emergency lighting required in warehouse applications is determined by the type of occupancy, the size and complexity of the site and the work undertaken. The mounting height of emergency luminaires is a major consideration. Access for maintenance will be needed, so ideally luminaires should be installed at manageable mounting heights, for example, on walls or clamped onto pillars using Dexion or similar brackets.
Emergency luminaires should meet the same standard of ingress protection as the general lighting. High and low ambient temperatures can be an issue for batteries in self-contained and maintained luminaires, so please contact our technical helpline for advice.
Thorlux offers a comprehensive range of emergency lighting control solutions from standalone emergency, through to full wireless control and monitoring systems.
The emergency lighting design must take into account the following:
- Escape route signs
- Stairs so that each flight receives direct light
- Changes in floor level
- Changes of escape route direction
- Corridor intersections
- First aid posts
- Fire alarm call points or pieces of fire fighting equipment
- Outside the final exit door and to a place of safety
- Moving stairways and walkways
- Toilet facilities exceeding 8 m² or any multiple closet facility without borrowed light
- Toilet facilities for disabled use
- Motor generator, control and plant rooms
- Manual release controls for electronically locked doors
- Escape equipment for disabled people
- Refuges and call points, including disabled toilet call positions
- All other areas as deemed by the Risk Assessment
Note: The majority of Thorlux luminaires are available with an integral emergency option including high output non-maintained luminaires ideal for greater mounting heights.
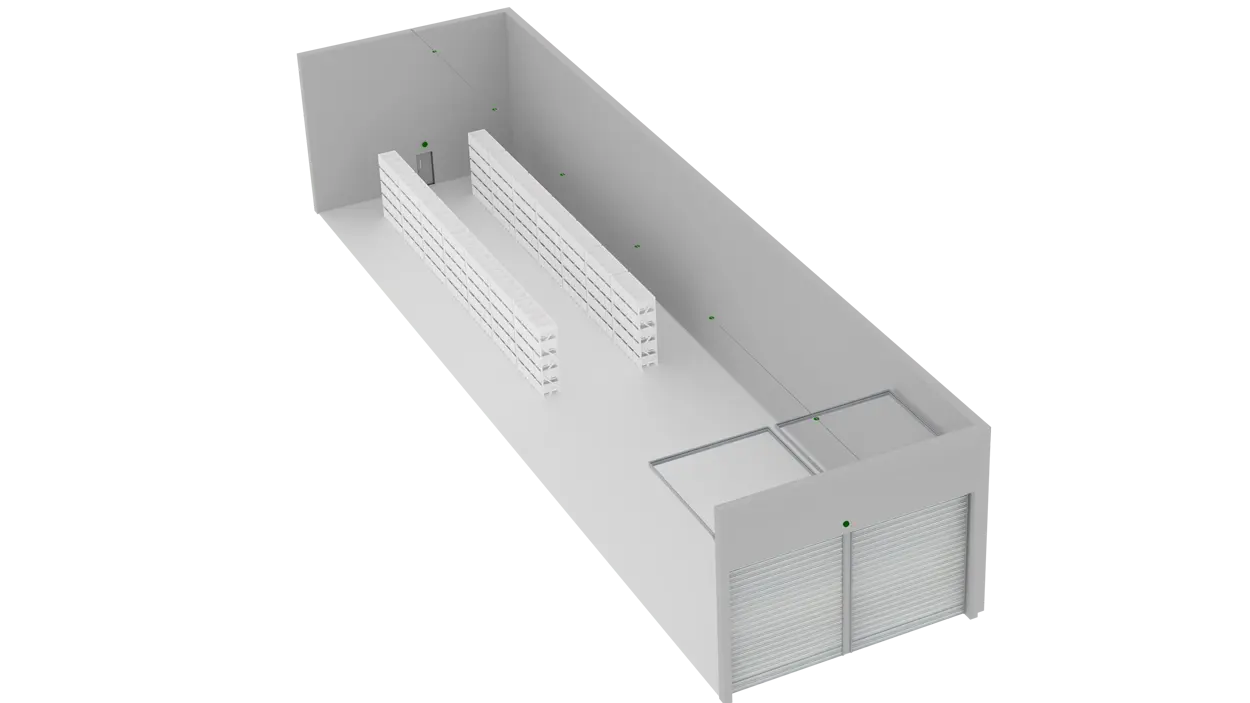